基于炉料结构及冶金性能的高炉透气性指数预测方法与流程
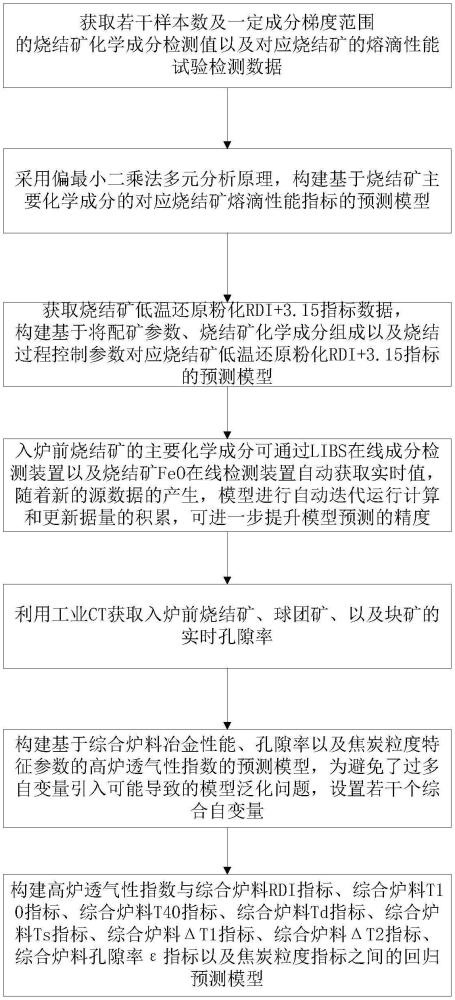
本发明涉及冶金,尤其涉及一种基于炉料结构及冶金性能的高炉透气性指数预测方法。
背景技术:
1、高炉透气性表示在一定条件下,炉内气流通过料层的能力,其直接决定了高炉煤气流分布是否合理,从而最终影响高炉生产是否稳定顺行。因此在高炉生产中,透气性的合理预判及有效控制作为最核心的操作环节之一,一直为炼铁工作者所关心。高炉透气性的变化与生产中的诸多因素有关,比如原燃料、送风、布料等都会对透气性产生影响。近些年来,随着高炉自动化程度的提高及管理水平的提升,高炉操作者逐渐重视起透气性的提前预判问题。但目前透气性预测方面的研究还存在着一些问题,如建立的模型仅具备离线计算,或者影响因素选取仅考虑局部且是固定参数,难以适应工业化应用等,因此在实际生产中,操作者对透气性的控制仍然大多凭经验,这对高炉的顺行产生不利影响。
2、目前,高炉入炉含铁炉料主要包括烧结矿、球团矿和块矿。含铁炉料良好的冶金性能是影响高炉透气性的关键因素,同时也是实现高炉强化冶炼和节能减排的重要前提。目前国内钢铁企业并未将高炉综合炉料熔滴试验列为常规检测,大部分企业仅检测烧结矿、球团矿和块矿等单种含铁炉料的熔滴性能,同时冶金性能试验成本较高且检测时间较长。因此,炼铁工作者难以根据炉料结构以及冶金性能的变化预知高炉透气性的变化趋势。
3、近年来,利用人工智能技术解决高炉复杂问题已广泛应用,因此构建基于炉料结构以及冶金性能的高炉透气性指数预测和预判,可为高炉炉料结构优化并提前制定合理的操作制度提供参考,同时也是实现低碳炼铁的重要举措。
4、专利(cn106777652a)公开了一种预测高炉透气性的方法,包括:采集高炉运行数据库的历史数据;分析历史数据并进行预处理,甄选历史数据得到符合生产要求的实际数据;获取当前时间段内高炉透气性的影响因子,并将影响因子按重要性的贡献大小进行权重排序;根据透气性影响因子权重排序结果建立对应的数据集;将数据集的影响因子按照透气性参数进行分类,计算每个类别中影响因子的中心;以黑箱模型建模为基础,建立若干个透气性预测子模型;根据需要将调整后的原燃料质量参数或操作控制参数按照其对应的类别数据输入至对应的透气性预测子模型;根据高炉运行数据库采集数据频率,动态采用最新数据对模型参数进行更新。该专利可动态更新透气性模型,提高了预测精度。
5、专利(cn 116124677a)公开了一种高炉烧结矿料层透气性的快速评价方法,步骤如下:对n个烧结料样品进行粒度分析;针对每组烧结矿样品分析数据进行计算机离散元建模,并进行均匀分布堆垛;对堆垛后的烧结矿料层进行统计,得到实体体积vi1/m3和堆垛体积vi0/m3,求取孔隙度ei;针对该在役高炉的全部烧结矿样品粒度组成,分别进行计算机建模,得到所有的孔隙度e1,e2,e3,……,en;用上述所有烧结矿样品的粒度组成和对应的孔隙度进行多元线性回归分析,得到孔隙度计算公式,计算并预测新的烧结矿样品的孔隙度。通过该方法,能够对烧结矿料层的透气性进行快速评价,给高炉操作调剂提供预警,提高了料层透气性判断和高炉操作调剂的科学性、合理性和准确性。
6、但关于基于炉料结构以及冶金性能的高炉透气性指数预测方法方面的专利未见报道。
技术实现思路
1、为解决以上问题,本发明提供一种基于炉料结构及冶金性能的高炉透气性指数预测方法,可为高炉炉料结构优化并提前制定合理的操作制度提供参考,同时也是实现低碳炼铁的重要举措。
2、本发明采用的技术方案是:一种基于炉料结构及冶金性能的高炉透气性指数预测方法,其特征在于:包括以下步骤:
3、s1、获取若干样本数的烧结矿化学成分检测值以及对应烧结矿的熔滴性能试验检测数据;
4、s2、采用偏最小二乘法多元分析原理构建基于烧结矿主要化学成分的对应烧结矿熔滴性能指标的预测模型a;
5、s3、获取烧结矿低温还原粉化rdi+3.15指标数据,构建基于将配矿结构参数、烧结矿化学成分组成以及烧结过程控制参数对应烧结矿低温还原粉化rdi+3.15指标的预测模型b;
6、s4、入炉前烧结矿的主要化学成分,通过libs在线成分检测装置以及烧结矿feo在线检测装置自动获取实际值,随着新的源数据的产生,预测模型a和预测模型b进行自动迭代运行计算和更新数据量的积累,提升预测模型a和预测模型b的精度;
7、s5、通过阶段性试验获得球团矿以及块矿的rdi+3.15指标以及对应的熔滴性能数值;
8、s6、获取入炉前烧结矿、球团矿、以及块矿的实时孔隙率;
9、s7、构建基于综合炉料冶金性能、孔隙率以及焦炭粒度特征参数的高炉透气性指数的预测模型c。
10、作为优选,步骤s1中,试验样本涵盖范围满足如下要求:即烧结矿sio2的质量分数为4.53%~6.09%;feo质量分数为6.59%~10.74%;al2o3质量分数为1.51%~3.17%;mgo质量分数为1.02%~2.65%;烧结矿r控制在1.72~2.35之间;其中烧结矿化学成分主要为:tfe、sio2、feo、al2o3、mgo以及烧结矿碱度r;对应烧结矿熔滴性能主要为:软化开始温度t10、软化终了温度t40、熔化开始温度ts、滴落温度td、软化区间δt1=t40-t10、熔化区间δt1=td-ts。
11、作为优选,步骤s2的具体步骤为:采用偏最小二乘法多元分析原理,将烧结矿主要成分参数:sio2、feo、al2o3、mgo以及r作为自变量,烧结矿高温软熔滴落性能各指标检测数据作为因变量进行多元回归,构建基于烧结矿主要化学成分的对应烧结矿熔滴性能指标的预测模型a。
12、作为优选,步骤s3的具体步骤为:获取烧结矿低温还原粉化rdi+3.15指标数据、烧结对应配矿结构、烧结矿主要成分以及烧结过程控制参数数据,将配矿结构参数、烧结矿化学成分组成、以及烧结过程控制参数作为自变量,烧结矿rdi+3.15检测数据作为因变量进行多元回归,构建基于将配矿结构参数、烧结矿化学成分组成以及烧结过程控制参数对应烧结矿低温还原粉化rdi+3.15指标的预测模型b。
13、作为优选,配矿结构参数为各堆混匀矿的配矿结构比例,烧结过程控制参数括废气温度、点火温度、返矿配比以及烧结过程负压。
14、作为优选,步骤s4中,开始软化温度t10的预测结果与实际值之间的相对误差为1.05%;软化结束温度t40的预测结果与实际值之间的相对误差为0.66%;滴落温度td的预测结果与实际值之间的相对误差为0.84%;开始熔化温度ts的预测结果与实际值之间的相对误差为0.32%;烧结矿软熔区间的预测结果与实际值之间的相对误差为6.70%;烧结矿熔化区间的预测结果与实际值之间的相对误差为6.79%;烧结矿rdi+3.15的预测结果与实际值之间的相对误差为3.60%。
15、作为优选,步骤s6中,利用工业ct获取入炉前烧结矿、球团矿、以及块矿的实时孔隙率,通过三维重建软件将扫描的切片数据进行处理,通过阈值分割提取上述烧结矿、球团矿、块矿的孔隙率。
16、作为优选,步骤s7的具体步骤为:构建基于综合炉料冶金性能、孔隙率以及焦炭粒度特征参数的高炉透气性指数的预测模型c,为避免了过多自变量引入导致的预测模型c泛化问题,设置若干个综合自变量,进一步构建高炉透气性指数与综合炉料rdi指标、综合炉料t10指标、综合炉料t40指标、综合炉料td指标、综合炉料ts指标、综合炉料δt1指标、综合炉料δt2指标、综合炉料孔隙率ε指标以及焦炭粒度指标之间的回归预测模型c,实现指导高炉操作调整以及前端烧结冶金性能的优化调整控制。
17、本发明取得的有益效果是:
18、1、目前,高炉入炉含铁炉料主要包括烧结矿、球团矿和块矿。一般来说目前炼铁厂高炉所使用的球团矿以及块矿的品种相对较为单一及其化学成分也相对稳定。故可通过阶段性试验获得球团矿以及块矿的rdi+3.15指标以及对应的熔滴性能(软化开始温度、软化终了温度、熔化开始温度、滴落温度、软化区间、熔化区间)数值;
19、2、入炉前烧结矿的主要化学成分可通过libs在线成分检测装置以及烧结矿feo在线检测装置自动获取实时值,随着新的源数据的产生,模型能够对上述预测公式进行自动迭代运行计算和更新,故随着数据量的积累,可进一步提升模型预测的精度。在样本空间下,开始软化温度t10的预测结果与实际值之间的相对误差为1.05%;软化结束温度t40的预测结果与实际值之间的相对误差为0.66%;滴落温度td的预测结果与实际值之间的相对误差为0.84%;熔化开始温度ts的预测结果与实际值之间的相对误差为0.32%;烧结矿软熔区间的预测结果与实际值之间的相对误差为6.70%;烧结矿熔化区间的预测结果与实际值之间的相对误差为6.79%;烧结矿rdi+3.15的预测结果与实际值之间的相对误差为3.60%。其模型预测结果误差较小,能够使用其模型对生产实际进行预测;
20、3、本发明基于炉料结构及冶金性能的高炉透气性指数预测模型,其预测±5‰的命中率达到92%以上,故此模型可为高炉实际操作调整提供参考依据。
技术研发人员:刘山平,丁晖,戚义龙,张晓萍,黄世来,刘益勇
技术所有人:马鞍山钢铁股份有限公司
备 注:该技术已申请专利,仅供学习研究,如用于商业用途,请联系技术所有人。
声 明 :此信息收集于网络,如果你是此专利的发明人不想本网站收录此信息请联系我们,我们会在第一时间删除