一种通过3D打印制造金属中空框体的方法及金属中空框体与流程
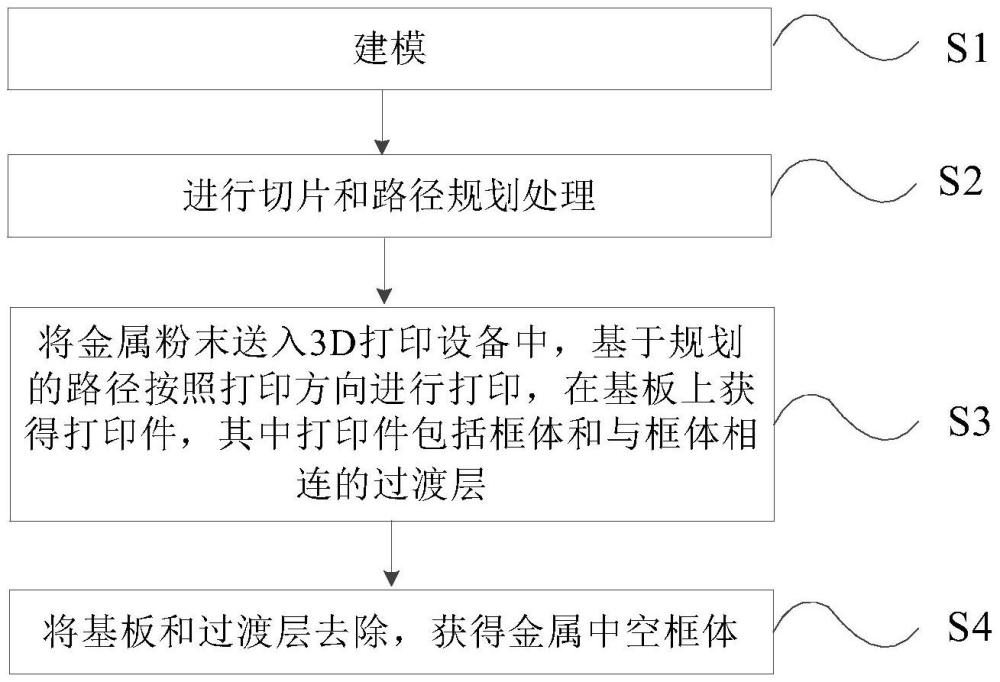
本技术涉及增材制造,具体地,涉及一种通过3d打印制造金属中空框体的方法及金属中空框体。
背景技术:
1、激光选区熔化作为3d打印技术一个重要分支,是一种能直接成型金属中空框体(例如手机中空框体)的高致密、高精度金属零件的快速成型技术,特别适合复杂中空框体结构零件的制造过程。相比于传统的锻造和精密铸造工艺,可节省大量原材料、缩短加工周期。
2、然而,由于激光超快速凝固过程中形成的收缩应力以及累积的热应力,通常仅可成形突显截面悬空伸出长度一般在0~2mm以内,再大将发生翘曲甚至断裂,无法完成零件打印,往往需要添加大量辅助支撑来完成大悬空截面的打印成形。支撑结构重量通常为零件重量的30~150%,导致材料利用率和打印效率大幅降低,增加零件制造成本,且降低零件量产性。因此,急需采用新工艺方案解决问题。
3、背景技术部分的内容仅仅是发明人所知晓的技术,并不当然代表本领域的现有技术。
技术实现思路
1、为了解决现有的上述技术问题,本技术的第一方面提供了一种通过3d打印制造金属中空框体的方法。待制造的所述金属中空框体包括至少三条边框和位于所述至少三条边框中相邻边框之间的连接部。所述方法包括:
2、建模,包括:
3、根据所述金属中空框体的结构建立本体打印模型;沿所述3d打印的打印方向,所述本体打印模型包括悬空部分,所述悬空部分对应所述金属中空框体的一条边框和位于所述一条边框两侧的两个连接部;
4、在在所述悬空部分的表面建立过渡层模型,其中所述过渡层模型朝向与所述打印方向相反的方向延伸;以及
5、将所述过渡层模型拆分为第一打印模型和第二打印模型,所述第一打印模型对应所述连接部,所述第二打印模型对应所述边框,
6、所述第二打印模型包括至少三个子打印模型;
7、进行切片和路径规划处理,包括:
8、分别对所述本体打印模型、所述第一打印模型和所述第二打印模型进行切片处理,获得多层本体切片层和至少七层过渡层切片层,其中每层过渡层切片层包括与所述第一打印模型对应的第一切片区域和与所述第二打印模型对应的第二切片区域,每个第二切片区域包括与所述至少三个子打印模型对应的至少三个边框切片子区域;其中所述至少七层过渡层切片层中的第二切片区域的厚度从所述至少七层过渡层切片层的第二层开始随着层数的增加先变大,后变小,直至与所述多层本体切片层中一层本体切片层的厚度相等;以及
9、对所述多层本体切片层和所述至少七层过渡层切片层进行线条扫描,从而完成路径规划处理;
10、将金属粉末送入3d打印设备中,基于规划的路径按照所述打印方向进行打印,在基板上获得打印件,其中所述打印件包括框体和与所述框体相连的过渡层;以及
11、将所述基板和所述过渡层去除,获得所述金属中空框体。
12、在本技术的一些实施例中,所述至少七层过渡层切片层的第二层中的第二切片区域的厚度为所述多层本体切片层中一层本体切片层的厚度的1~3倍,所述至少七层过渡层切片层的第三层至第六层中每层的第二切片区域的厚度为所述多层本体切片层中一层本体切片层的厚度的1~2倍,所述至少七层过渡层切片层的第七层中的第二切片区域的厚度与所述多层本体切片层中一层本体切片层的厚度相等。
13、在本技术的一些实施例中,所述过渡层模型的厚度为0.3~3.5mm,所述过渡层模型朝向与所述打印方向相反的方向延伸的长度为0.5~5.5mm,所述连接部包括r角和/或c角,所述r角的半径为0.5~6.5mm,所述c角的角度为45°~75°;
14、所述子打印模型的个数为3~7个,每个子打印模型的长度≤65mm。
15、在本技术的一些实施例中,所述多层本体切片层中一层本体切片层的厚度为20~100μm,每层过渡层切片层中的所述第一切片区域和所述第二切片区域的重叠宽度为0.05~0.15mm,相邻切片子区域的重叠宽度为0.05~0.15mm;
16、所述至少三个边框切片子区域包括第一边框切片子区域、第二边框切片子区域和位于所述第一边框切片子区域和所述第二边框切片子区域中间的第三边框切片子区域,所述第一边框切片子区域和所述第二边框切片子区域分别与所述第一切片区域相邻;
17、每个本体切片层均包括第一实体部分和第一轮廓部分,每个第一切片区域均包括第二实体部分和第二轮廓部分,每个边框切片子区域均包括第三实体部分和第三轮廓部分;
18、对所述多层本体切片层和所述至少七层过渡层切片层进行线条扫描时,所述第一轮廓部分与所述第一实体部分光斑补偿0.06~0.15mm,所述第二轮廓部分与所述第二实体部分光斑补偿0.06~0.15mm,所述第三轮廓部分与所述第三实体部分光斑补偿0.1~0.15mm。
19、在本技术的一些实施例中,对所述多层本体切片层进行线条扫描时,所述多层本体切片层的第一层的扫描角度为30°~70°,所述多层本体切片层的其他层的扫描角度在前一层的扫描角度上增加50°~90°;
20、对所述至少七层过渡层切片层进行线条扫描时,所述至少七层过渡层切片层的第一层的扫描角度为30°~70°,所述至少七层过渡层切片层的其他层的扫描角度在前一层的扫描角度上增加50°~90°。
21、在本技术的一些实施例中,将金属粉末送入3d打印设备中,基于规划的路径按照所述打印方向进行打印,在基板上获得打印件包括:
22、设定所述3d打印设备的激光参数;以及
23、将所述金属粉末送入所述3d打印机中,在惰性气体氛围下,按照所述打印方向,先基于所述多层本体切片层的规划路径在所述基板上打印所述框体的未与所述过渡层相连的部分,然后基于所述至少七层过渡层切片层的规划路径打印所述过渡层,接着再基于所述多层本体切片层的规划路径在所述过渡层上打印所述框体的剩余部分,获得位于所述基板上的所述打印件。
24、在本技术的一些实施例中,设定所述3d打印设备的激光参数包括:
25、分别设定对应所述第一实体部分、所述第一轮廓部分、所述第二实体部分、所述第二轮廓部分、所述至少七层过渡层切片层的第一层至第六层的第三实体部分、所述至少七层过渡层切片层的第一层至第六层的第三轮廓部分的激光参数;以及
26、设定所述至少七层过渡层切片层的其他层的激光参数,使得所述至少七层过渡层切片层的其他层的激光参数在前一层的基础上改变不超过20%,直至与所述第一实体部分和所述第一轮廓部分的激光参数相同。
27、在本技术的一些实施例中,对所述第一实体部分设置的激光参数包括激光功率:150~320w、激光扫描速度:800~1500mm/s、激光扫描间距:0.05~0.15mm;对所述第一轮廓部分设置的激光参数包括激光功率:150~280w、激光扫描速度:400~1200mm/s;
28、对所述第二实体部分设置的激光参数包括激光功率:150~320w、激光扫描速度:800~1500mm/s、激光扫描间距:0.05~0.15mm;对所述第二轮廓部分设置的激光参数包括激光功率:150~280w、激光扫描速度:400~1200mm/s;
29、对所述至少七层过渡层切片层的第一层至第六层的第一边框切片子区域和第二边框切片子区域的第三实体部分设置的激光参数包括激光功率:40~130w、激光扫描速度:400~2500mm/s、激光扫描间距:0.03~0.08mm;对所述至少七层过渡层切片层的第一层至第六层的第一边框切片子区域和第二边框切片子区域的第三轮廓部分设置的激光参数包括激光功率:40~100w;激光扫描速度:500~1800mm/s;
30、对所述至少七层过渡层切片层的第一层至第六层的第三边框切片子区域的第三实体部分设置的激光参数包括激光功率:20~110w、激光扫描速度:600~2500mm/s、激光扫描间距:0.03~0.07mm;对所述至少七层过渡层切片层的第一层至第六层的第三边框切片子区域的第三轮廓部分设置的激光参数包括激光功率:40~100w;激光扫描速度:500~1800mm/s。
31、在本技术的一些实施例中,设定所述3d打印设备的激光参数还包括:
32、设定所述3d打印机的光斑直径范围和基板温度;
33、其中所述光斑直径范围为50~90μm,所述基板温度为25~200℃。
34、在本技术的一些实施例中,所述金属中空框体包括四条边框和四个连接部,所述金属粉末为钛合金粉末,所述钛合金粉末的粒径范围:15~85μm,粉末氧含量≤1300ppm,粉末流动性≤35s/50g。
35、在本技术的一些实施例中,所述的方法还包括:
36、将所述基板和所述打印件进行真空退火,包括:
37、在真空度<10-3pa的情况下,先将所述基板和所述打印件以<5℃/min的第一升温速度升温至300~500℃,并保温1~2h;然后以<3℃/min的第二升温速度升温至550℃~850℃,并保温4~15h;保温结束后,随炉缓慢冷却至室温。
38、本技术的第二方面提供了利用上述方法制得的金属中空框体。
39、本技术通过将过渡层切片层的第二层至第七层的厚度设置为先增加后减小至与一层本体切片层的厚度相等,能够降低当前打印层的热输入,同时减少对已成形层的热应力输入,降低翘曲开裂风险,为后续本体常规能量输入打印提供稳定的导热层及应力分散空间,提高打印件的成型质量,最终实现中空框体无支撑3d打印成型。
40、本技术的附加方面和优点将在下面的描述中部分给出,部分将从下面的描述中变得明显,或通过本技术的实践了解到。
技术研发人员:沈旺,罗楚贵,陆声培,沈治军
技术所有人:东莞九思增材制造有限公司
备 注:该技术已申请专利,仅供学习研究,如用于商业用途,请联系技术所有人。
声 明 :此信息收集于网络,如果你是此专利的发明人不想本网站收录此信息请联系我们,我们会在第一时间删除