桥式起重机主梁T形钢与腹板对接装置及对接方法与流程
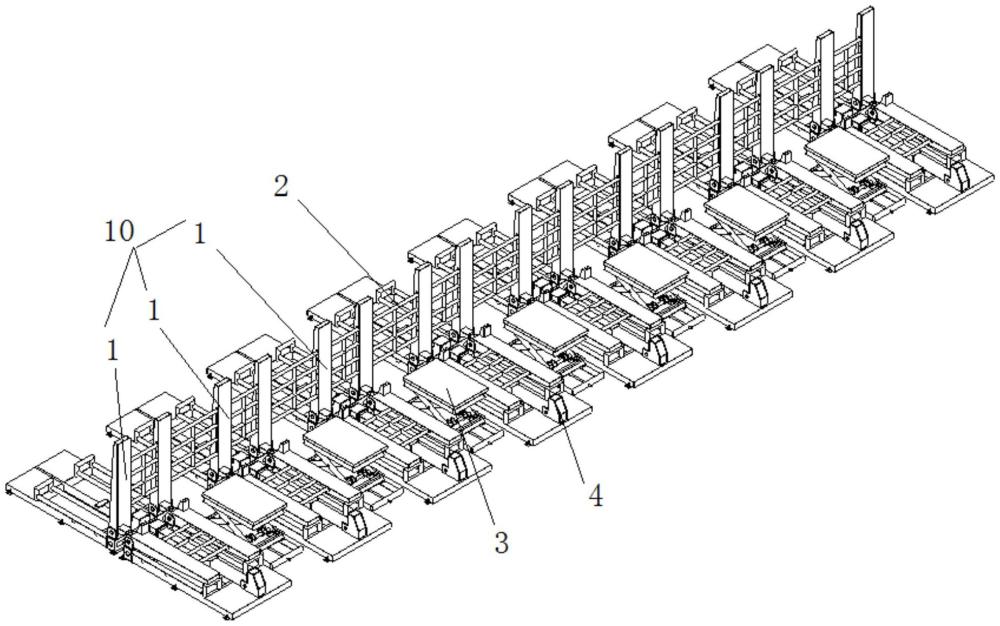
本发明属于主梁对接,尤其涉及一种桥式起重机主梁t形钢与腹板对接装置及对接方法。
背景技术:
1、桥架主梁是桥式起重机的关键承载部件,具有尺寸长、截面积大、结构复杂、焊接量大等特点。常见t形钢承轨箱形主梁主要由轨道、上盖板、下盖板、主腹板、副腹板、大筋板、t形钢等组成;
2、由于桥式起重机主梁腹板、盖板尺寸长(一般为20-30米)且柔软,因此需多块钢板对接形成腹板或盖板,目前现有技术中桥架主梁在通过钢板对接形成腹板或盖板和t形钢与腹板对接形成主梁过程中,采用行车加专用工装起吊。起吊后钢板翻身摆幅大,且需要多人进行配合,整体对接过程自动化程度低,从而造成人力物力投入大,严重影响了主梁制造周期。
技术实现思路
1、为至少部分地解决上述现有技术中存在的技术问题,本发明提供一种桥式起重机主梁t形钢与腹板对接装置及对接方法。
2、本发明的技术方案如下:
3、第一方面,本发明提供了一种桥式起重机主梁t形钢与腹板对接装置包括液压翻转机构、液压系统、翻转连接架、钢板起升装置和t形钢与腹板对接装置,其中:所述液压翻转机构由多个翻转单元排列设置,所述液压系统控制于所述翻转机构上每个所述翻转单元翻转,所述翻转连接架长度可调的连接于所述翻转单元一侧,所述钢板起升装置设置在所述翻转单元之间与所述翻转连接架对应,所述t形钢与腹板对接装置设置在所述翻转单元中部通过所述液压系统控制;
4、所述翻转单元包括支撑底架和两个翻转架,两个所述翻转架可转动的对称设置在所述支撑底架上。
5、进一步地,在所述桥式起重机主梁t形钢与腹板对接装置中,所述钢板起升装置包括起升底架、滑动导轨、升降平台、剪叉支架和剪叉转轴,所述滑动导轨分别设置在所述起升底架与所述升降平台同一侧,所述剪叉支架底部一侧与所述起升底架通过所述滑动导轨滑动连接,所述剪叉支架底部另一侧与所述起升底架转动连接,所述剪叉支架中部通过所述剪叉转轴转动连接,所述剪叉支架顶部一侧与所述升降平台通过所述滑动导轨滑动连接,所述剪叉支架顶部另一侧与所述升降平台转动连接,所述剪叉支架用于实现平台升降。
6、进一步地,在所述桥式起重机主梁t形钢与腹板对接装置中,所述翻转连接架两端通过螺栓分别与所述翻转单元之间对应所述钢板起升装置一侧所述翻转架固定连接。
7、进一步地,在所述桥式起重机主梁t形钢与腹板对接装置中,所述t形钢与腹板对接装置包括直角头、滑台和液压油缸,所述滑台设置在其中一个所述支撑底架中部,所述直角头滑动设置在所述滑台上,所述液压油缸安装在所述支撑底架上与所述液压系统连接,所述液压油缸输出端与所述直角头连接。
8、进一步地,在所述桥式起重机主梁t形钢与腹板对接装置中,所述钢板起升装置还包括轨道架,所述起升底架可滑动设置在所述轨道架上,所述轨道架用于实现钢板起升装置的位置调整。
9、进一步地,在所述桥式起重机主梁t形钢与腹板对接装置中,所述液压翻转机构还包括电气控制系统,所述电气控制系统用于控制所述液压系统操作翻转架实施翻转以及t形钢与腹板对接装置实施对接。
10、第二方面,本发明还提供了一种桥式起重机主梁t形钢与腹板对接方法,包括:
11、s1:通过电磁吊具将主梁盖板、腹板对接钢板放置在带有t形钢与腹板对接装置的翻转架上,通过t形钢与腹板对接装置的t型钢与腹板对接位置,辅助调整对接钢板的位置,保证对接钢板宽度方向错边小于1mm,上下错边小于0.5mm,采用埋弧焊接施焊;
12、s2:启动液压系统,并操作电气控制系统控制液压系统使翻转架带动主梁盖板、腹板对接钢板开始翻转,翻转动作完成后,通过电气控制系统控制液压系统使翻转架复位,此时工人对主梁盖板、腹板对接钢板焊缝清根,并进行第二次埋弧焊接施焊;
13、s3:施焊间隙工人吊主梁其他盖板、腹板,进行钢板对接及埋弧焊接;
14、s4:钢板对接施焊完成后,通过控制钢板起升装置,使钢板脱离翻转架,待钢板升高到一定高度时,通过专业的坡口切割设备对腹板上拱进行切割,腹板切割完成后,控制钢板起升装置使钢板下降落至翻转架上;
15、s5:吊t形钢于t形钢与腹板对接装置的直角头处,并找正t形钢于腹板高度;
16、s6:计算出t形钢最大变形量以及各处t形钢与腹板对接装置动作变形量,通过对液压系统输入相应的系数,自动控制液压缸使直角头沿滑台运动,其中每个翻转单元上的t形钢与腹板对接装置动作顺序一定是从中间向两侧依次运动,运动区间内t形钢与腹板上拱逐步一致,工人对其进行点焊,
17、s7:t形钢与腹板点焊完成,进行埋弧焊接,焊接完成后通过液压翻转机构翻身,对另一面进行焊接,从而完成桥式起重机主梁t形钢与腹板对接。
18、进一步地,在所述桥式起重机主梁t形钢与腹板对接方法中,在s6中,t形钢最大变形量δf可根据公式得出:当桥式起重机跨距l=15~30m时,δf=(0.25~0.45)l,当桥式起重机跨距l=30~40m时,δf=(0.5~0.8)l,具体系数选择可根据实际切割腹板上拱时的变形系数选择;根据上述公式,通过在系统中输入相应系数,可计算处t形钢最大变形量,再根据最大变形量计算出各处t形钢与腹板对接装置动作变形量。
19、本发明的桥式起重机主梁t形钢与腹板对接装置及对接方法具有如下优点和有益效果:
20、桥式起重机主梁t形钢与腹板对接装置结构简单、便于操作,利用该桥式起重机主梁t形钢与腹板对接装置实施的桥式起重机主梁t形钢与腹板对接方法,操作便捷,可实现自动化对接,通过液压翻转机构提供翻转力,使主梁在焊接时实现翻转,提高了对接效率,通过t形钢与腹板对接装置的配合有效提高了对接精度,同时有效缩减了主梁制造周期。
技术特征:
1.一种桥式起重机主梁t形钢与腹板对接装置,其特征在于,所述桥式起重机主梁t形钢与腹板对接装置包括液压翻转机构、液压系统、翻转连接架、钢板起升装置和t形钢与腹板对接装置,其中:所述液压翻转机构由多个翻转单元排列设置,所述液压系统控制于所述翻转机构上每个所述翻转单元翻转,所述翻转连接架长度可调的连接于所述翻转单元一侧,所述钢板起升装置设置在所述翻转单元之间与所述翻转连接架对应,所述t形钢与腹板对接装置设置在所述翻转单元中部通过所述液压系统控制;
2.根据权利要求1所述的桥式起重机主梁t形钢与腹板对接装置,其特征在于,所述钢板起升装置包括起升底架、滑动导轨、升降平台、剪叉支架和剪叉转轴,所述滑动导轨分别设置在所述起升底架与所述升降平台同一侧,所述剪叉支架底部一侧与所述起升底架通过所述滑动导轨滑动连接,所述剪叉支架底部另一侧与所述起升底架转动连接,所述剪叉支架中部通过所述剪叉转轴转动连接,所述剪叉支架顶部一侧与所述升降平台通过所述滑动导轨滑动连接,所述剪叉支架顶部另一侧与所述升降平台转动连接,所述剪叉支架用于实现平台升降。
3.根据权利要求1所述的桥式起重机主梁t形钢与腹板对接装置,其特征在于,所述翻转连接架两端通过螺栓分别与所述翻转单元之间对应所述钢板起升装置一侧所述翻转架固定连接。
4.根据权利要求1所述的桥式起重机主梁t形钢与腹板对接装置,其特征在于,所述t形钢与腹板对接装置包括直角头、滑台和液压油缸,所述滑台设置在其中一个所述支撑底架中部,所述直角头滑动设置在所述滑台上,所述液压油缸安装在所述支撑底架上与所述液压系统连接,所述液压油缸输出端与所述直角头连接。
5.根据权利要求2所述的桥式起重机主梁t形钢与腹板对接装置,其特征在于,所述钢板起升装置还包括轨道架,所述起升底架可滑动设置在所述轨道架上,所述轨道架用于实现钢板起升装置的位置调整。
6.根据权利要求1所述的桥式起重机主梁t形钢与腹板对接装置,其特征在于,所述液压翻转机构还包括电气控制系统,所述电气控制系统用于控制所述液压系统操作翻转架实施翻转以及所述t形钢与腹板对接装置实施对接。
7.一种利用根据权利要求1至6中任一项所述的桥式起重机主梁t形钢与腹板对接装置实施的对接方法,其特征在于,包括:
8.根据权利要求1所述的桥式起重机主梁t形钢与腹板对接方法,其特征在于,在s6中,t形钢最大变形量δf可根据公式得出:当桥式起重机跨距l=15~30m时,δf=(0.25~0.45)l,当桥式起重机跨距l=30~40m时,δf=(0.5~0.8)l,具体系数选择可根据实际切割腹板上拱时的变形系数选择;根据上述公式,通过在系统中输入相应系数,可计算处t形钢最大变形量,再根据最大变形量计算出各处t形钢与腹板对接装置动作变形量。
技术总结
本发明公开了一种桥式起重机主梁T形钢与腹板对接装置及对接方法,桥式起重机主梁T形钢与腹板对接装置包括液压翻转机构、液压系统、翻转连接架、钢板起升装置和T形钢与腹板对接装置,液压翻转机构由多个翻转单元排列设置,液压系统控制于翻转机构上每个翻转单元翻转,翻转连接架长度可调的连接于翻转单元一侧,钢板起升装置设置在翻转单元之间与翻转连接架对应,T形钢与腹板对接装置设置在翻转单元中部通过液压系统控制。本发明实现了主梁腹板、盖板钢板对接、钢板翻身及腹板切割上拱、T形钢与腹板对接可在同一设备中进行,同时T形钢实现自动化从中间向两端弯曲变形,节省了人力物力,提高了主梁装焊精度及效率,有效缩短了主梁制造周期。
技术研发人员:岳海豹,朱东科,平萍,白崇玉,周继红,吴泽波,王炯,赵海军,赵永刚,任增斌,李海峰,冯志飞
受保护的技术使用者:太原重工股份有限公司
技术研发日:
技术公布日:2024/11/14
技术研发人员:岳海豹,朱东科,平萍,白崇玉,周继红,吴泽波,王炯,赵海军,赵永刚,任增斌,李海峰,冯志飞
技术所有人:太原重工股份有限公司
备 注:该技术已申请专利,仅供学习研究,如用于商业用途,请联系技术所有人。
声 明 :此信息收集于网络,如果你是此专利的发明人不想本网站收录此信息请联系我们,我们会在第一时间删除