一种涡轮壳体结构的制作方法
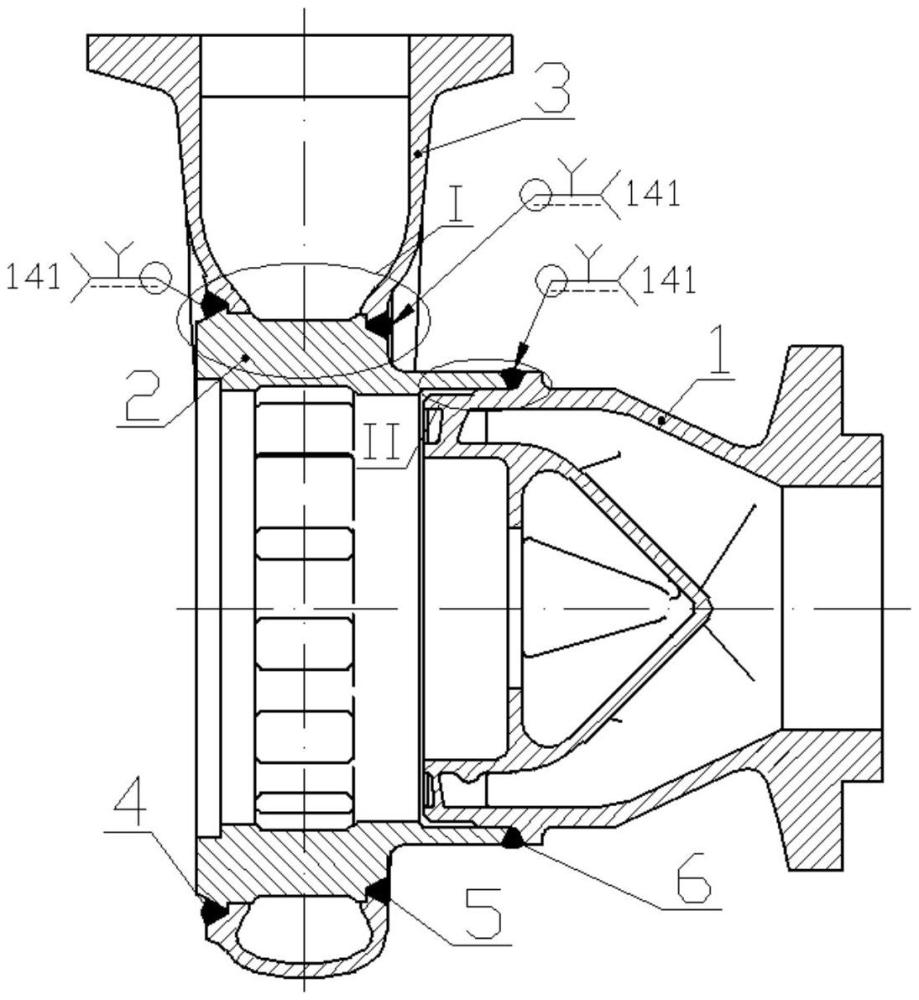
本发明涉及一种涡轮壳体结构,特别涉及液体火箭发动机涡轮壳体结构,属于液体火箭发动机涡轮泵。
背景技术:
1、在液体火箭发动机涡轮泵中,涡轮壳体是承受高温、高压和复杂振动载荷的重要部件。尤其是对补燃循环发动机,涡轮壳体工作压力高、结构复杂,一般采用多个零件拼焊的方式成形,焊缝数量多,失效风险大,是影响涡轮泵结构可靠性的重要因素。同时,现阶段的液体火箭发动机研制周期短、生产加工进度紧,若要保证产品性能的一致性,对于设计及生产加工难度较大。
2、传统设计方案一般采用多个零件拼焊构成整个涡轮壳体。一般包括涡轮进口管(1)法兰、外壁、锥形导流管、涡轮静子、出口法兰、集合器和导流栅等零部组件,各部分零件一般采用锻件、板材等方式加工,而静子叶片主要采用铸造的方式加工。各零件采用拼焊的方式构成涡轮壳体组件,再装配至涡轮泵上。
3、上述涡轮壳体结构存在两个问题:一是焊缝数量较多,在焊接时难以保证各零组件的变形程度,造成涡轮性能的一致性相对较差;二是出口管壳体采用两半管和出口管嘴拼焊的方式成形,存在一条较长的纵焊缝和两处交叉焊缝,结构复杂,可靠性与一致性相对较低;三是各零组件在拼焊时,将会产生较多的死腔,存在多余物风险,给发动机工作带来隐患;四是构成涡轮壳体的零组件较多,加工生产周期较长,不利于快节奏的发动机研制。
4、针对传统拼焊方案的问题,存在一种基于3d打印的设计方案,即利用3d打印的方法,将涡轮壳体整体打印出来,从而避免多零件拼焊。但此方案仍存在一个致命问题:对于存在空腔的结构,3d打印工艺需要支撑结构对内壁进行支撑;而为了解决出口管内3d打印的支撑无法去除的问题,须将出口管设计为水滴形自支撑结构,但该结构将会带来较大的应力集中和流动损失,在高温高压的涡轮壳体内,导致涡轮性能和结构可靠性大大降低,无法使用。
5、综上,现有技术存在以下问题:
6、1)传统涡轮壳体结构焊缝数量较多在焊接时难以保证各零组件的变形程度,造成涡轮性能的一致性相对较差;
7、2)出口管壳体采用两半管和出口管嘴拼焊的方式成形,存在一条较长的纵焊缝和两处交叉焊缝,此种类型的焊缝由于结构复杂,可靠性与一致性相对较低;
8、3)各零组件在拼焊时,将会产生较多的死腔,存在多余物风险,给发动机工作带来隐患;
9、4)构成涡轮壳体的零组件较多,且需要在各个车间反复传递,加工生产周期较长,不利于快节奏的发动机研制;
10、5)对于整体3d打印的方法加工,须将出口管设计为水滴形自支撑结构以满足3d打印工艺性要求,但该结构将会带来较大的应力集中和流动损失,在高温高压的涡轮壳体内,导致涡轮性能和结构可靠性大大降低。
技术实现思路
1、本发明的技术解决问题是:克服现有技术的不足,提供一种涡轮壳体结构,涡轮性能一致性好。
2、本发明的技术解决方案是:
3、本发明公开了一种涡轮壳体结构,包括:进口管、出口管和导流叶栅;其中,
4、所述进口管、出口管、导流叶栅组成燃气通道,通过焊接的方式组成涡轮壳体,进口管与上游燃气发生器相连接,出口管与下游燃气弯管相连接;
5、进口管包括壳体、导流锥和涡轮静子,为整体3d打印成型;涡轮静子与壳体的一端连接;壳体为回转腔体,导流锥置于回转腔体内,与涡轮静子连接;
6、进口管与导流叶栅之间的空腔内安装涡轮转子。;
7、导流叶栅包括若干导流叶片,为整体3d打印成型;
8、燃气发生器产生的高温燃气,经过进口管内导流锥整流及涡轮静子加速后进入涡轮转子的叶片通道;对涡轮转子做功后,在导流叶片的作用下显著削弱旋流,最终在出口管的导向下进入下游燃气弯管和推力室。
9、进一步地,在上述结构中,所述进口管,还包括支撑筋板和进口法兰;其中,
10、所述进口管从涡轮静子向进口法兰方向逐渐打印成型,3d打印支撑面为涡轮静子的出口端面成型;进口法兰位于壳体远离涡轮静子的一端;
11、所述支撑筋板连接在壳体与导流锥之间以及导流锥内部,用于加强壳体与导流锥的结构强度。
12、进一步地,在上述结构中,所述壳体为回转体,包括扩张段和与进口法兰相连的平直段,扩张段为自支撑结构,扩张段与水平方向的夹角γ为50~70°。
13、进一步地,在上述结构中,所述导流锥为空腔结构,导流锥顶角θ=85°~90°,内圆角半径r=1~3mm。
14、进一步地,在上述结构中,所述安装在壳体与导流锥之间的支撑筋板的后缘角度α=50~70°,安装在导流锥内部的后缘角度β=50~70°。
15、进一步地,在上述结构中,所述导流叶栅从空腔结构的尾部向与进口管连接处打印成型。
16、进一步地,在上述结构中,若干导流叶片均布在空腔结构四周,另设置两片矩形支撑筋板平行于气流出口方向,其前、尾缘倒圆半径均为r',长度为半径r'的5~6倍。
17、进一步地,在上述结构中,所述导流叶栅与进口管连接处采用坡口锁底焊接,在非焊接定位段设置径向间隙,径向间隙的宽度m1=1~2mm。
18、进一步地,在上述结构中,所述出口管包括出口法兰和集合器;出口管为整体3d打印成型,由出口法兰向集合器远离出口法兰一端打印成型;
19、所述集合器外廓为偏心圆结构,包括内圆和外圆;内圆和外圆之间形成腔体;内圆的圆心位于外圆圆心远离出口法兰一侧,两个圆心的距离x为1/6r”~1/3r”;小外圆半径为1/3r”~2/3r”,r”为大外圆半径。
20、进一步地,在上述结构中,所述出口管与导流叶栅连接的第一环焊缝和第二环焊缝设置在不同的径向位置,第二环焊缝的锁底在导流叶栅上,第一环焊缝的锁底在出口管上;焊接时将导流叶栅沿轴线推入导流叶栅与出口管接触面。
21、本发明与现有技术的有益效果在于:
22、(1)本发明采用3d打印技术,实现了涡轮壳体内形面加工稳定性较好的技术效果,解决了传统涡轮壳体结构焊缝数量较多,在焊接时难以保证各零组件变形程度,涡轮性能一致性相对较差的技术问题;
23、(2)本发明采用3d打印技术,实现了涡轮出口管一体化成型的技术效果,解决了采用两半管和出口管嘴拼焊方式成形,导致焊缝结构复杂,可靠性相对较低的技术问题;
24、(3)本发明采用3d打印技术,实现了大量减少焊缝数量的技术效果,解决了各零组件拼焊时产生较多死腔,增加多余物隐患的技术问题。
25、(4)本发明采用3d打印与焊接相结合的方案,实现了壳体快速成型的技术效果,解决了由于涡轮壳体的零组件较多,需要在各个车间反复传递,加工生产周期较长的技术问题,加快了发动机研制的节奏;
26、(5)本发明采用3d打印与焊接相结合的方案,实现了复杂壳体加工成型的技术效果,解决了整体3d打印无法去除支撑,或采用自支撑结构应力集中和流动损失较大的技术问题。
技术特征:
1.一种涡轮壳体结构,其特征在于,包括:进口管(1)、出口管(3)和导流叶栅(2);其中,
2.根据权利要求1所述的一种涡轮壳体结构,其特征在于:所述进口管(1)与导流叶栅(2)之间设置的空腔安装涡轮转子。
3.根据权利要求1所述的一种涡轮壳体结构,其特征在于:所述进口管(1),还包括支撑筋板(1-3)和进口法兰(1-5);其中,
4.根据权利要求3所述的一种涡轮壳体结构,其特征在于:所述壳体(1-2)为回转体,包括扩张段和与进口法兰(1-5)相连的平直段,扩张段为自支撑结构,扩张段与水平方向的夹角γ为50~70°。
5.根据权利要求3所述的一种涡轮壳体结构,其特征在于:所述导流锥(1-1)为空腔结构,导流锥(1-1)顶角θ=85°~90°,内圆角半径r=1~3mm。
6.根据权利要求3所述的一种涡轮壳体结构,其特征在于:连接在壳体(1-2)与导流锥(1-1)之间的支撑筋板(1-3)的后缘角度α=50~70°,安装在导流锥(1-1)内部的后缘角度β=50~70°。
7.根据权利要求5所述的一种涡轮壳体结构,其特征在于:所述导流叶栅(2)为3d打印成型,从空腔结构的尾部向与进口管(1)连接处打印。
8.根据权利要求6所述的一种涡轮壳体结构,其特征在于:若干导流叶片均布在空腔结构四周,另设置两片矩形支撑筋板平行于气流出口方向,其前、尾缘倒圆半径均为r',长度为半径r'的5~6倍。
9.根据权利要求1所述的一种涡轮壳体结构,其特征在于:所述导流叶栅(2)与进口管(1)连接处采用坡口锁底焊接,在非焊接定位段设置径向间隙,径向间隙的宽度m1=1~2mm。
10.根据权利要求1所述的一种涡轮壳体结构,其特征在于:所述出口管(3)包括出口法兰和集合器;由出口法兰向集合器远离出口法兰一端打印成型;
技术总结
本发明公开了一种涡轮壳体结构,包括:进口管、出口管和导流叶栅;其中,所述进口管、出口管、导流叶栅组成燃气通道,通过焊接的方式组成涡轮壳体,进口管与上游燃气发生器相连接,出口管与下游燃气弯管相连接;进口管包括壳体、导流锥和涡轮静子;涡轮静子与壳体的一端连接;壳体为回转腔体,导流锥置于回转腔体内,与涡轮静子连接;进口管与导流叶栅之间的空腔安装涡轮转子;导流叶栅包括若干导流叶片;燃气发生器产生的高温燃气,经过进口管内导流锥整流及涡轮静子加速后进入涡轮转子的叶片通道,驱动涡轮转子做功后,在导流叶片的作用下显著削弱旋流,最终经出口管导向进入下游燃气弯管和推力室。
技术研发人员:安近怀远,叶树波,徐楠,尉星航,郭鑫,李瑜,安莎
受保护的技术使用者:西安航天动力研究所
技术研发日:
技术公布日:2024/11/14
技术研发人员:安近怀远,叶树波,徐楠,尉星航,郭鑫,李瑜,安莎
技术所有人:西安航天动力研究所
备 注:该技术已申请专利,仅供学习研究,如用于商业用途,请联系技术所有人。
声 明 :此信息收集于网络,如果你是此专利的发明人不想本网站收录此信息请联系我们,我们会在第一时间删除